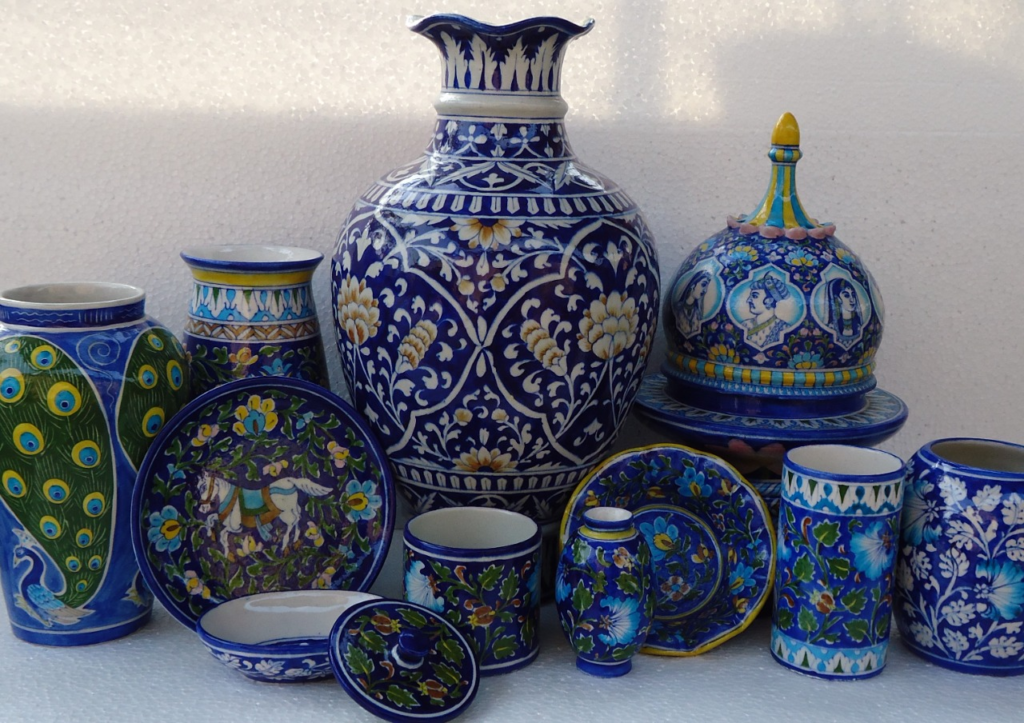
India is a country rich in heritage and arts. There are many famous Indian ancient arts that are also continued making till now. One is Blue Pottery. It is an ancient art, from Rajasthan, Jaipur. In this topic, we will discuss what blue pottery is and how it is created.
Blue Pottery
Blue pottery is usually considered a typical Jaipuri skill despite having Turko-Persian roots. The pottery was colored with a special blue dye, which is why it is called “blue pottery.” Quartz is used to make blue pottery. It is not created with clay like other potteries.
The material used to make Blue Pottery is raw glaze, sodium sulfate, Quartz, and Multani mitti (fuller’s earth). It is roasted just once, like pottery. The prior advantage of blue pottery is that it never cracks. It is also waterproof, clean, and suitable for daily usage. When the pot is rotated, the brush artistically decorates blue pottery.
The material used to make Blue Pottery is raw glaze, sodium sulfate, Quartz, and Multani mitti (fuller’s earth). It is roasted just once, like pottery. The prior advantage of blue pottery is that it never cracks. It is also waterproof, clean, and suitable for daily usage. When the pot is rotated, the brush artistically decorates blue pottery.
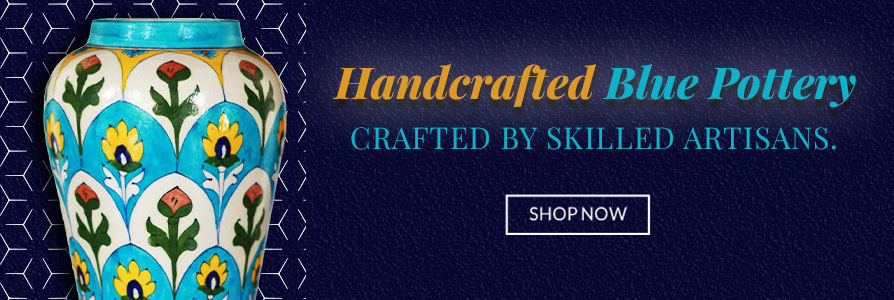
By blending copper oxide with salt or sugar in a kiln and then filtering the mixture, the blue or turquoise tint is created. Cobalt oxide is used to create the dark ultramarine color. Arabesque patterns from the Mugal era and animal and bird motifs are the sources of the prevalent motifs.
The craft is primarily found in Jaipur. Blue Pottery Pitcher – White Floral is a beautiful piece of Blue Pottery. There are many products made in blue pottery like plates, flower vases, pottery pots, etc.
The craft is primarily found in Jaipur. Blue Pottery Pitcher – White Floral is a beautiful piece of Blue Pottery. There are many products made in blue pottery like plates, flower vases, pottery pots, etc.
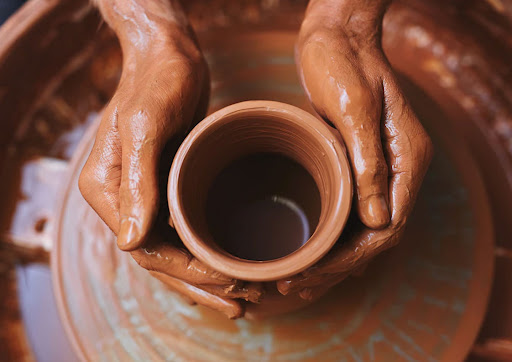
The Process of Making Blue Pottery
The process of creating blue pottery is very time-consuming and tough. It includes many stages, from making the dough for pottery to firing. It is a very long process.
Creating The Dough
Raw materials that are used to create the dough for Blue Pottery are quartz powder, Multani Mitti, shattered glass, Katria Gond, and Saaji. After choosing the raw material, Saaji, Katria Gond, leftover glass, and Multani Mitti must first be crushed and ground into a fine powder. These uncooked ingredients are then precisely weighed and mixed with water on a spotless surface. When well combined, a non-sticky dough is produced, and it is then allowed to rest for at least 7-8 hours before being utilized.
Constructing The Mold
Plaster of Paris is used to create molds. The desired forms and sizes are created as molds, which are subsequently dried. It is cast in molds to prevent cracking because using dough has its limitations. Particular goods, like vases, are made using one or two molds, and the castings are joined together with a little dough and water. If properly cared for, the molds can be utilized more often.
Making The Product
A small amount of the created pottery dough is taken and flattened like a round tortilla. Then the flattened dough is placed on the mold. The mold is then continuously wiggled by the artist to set the dough properly inside it.
When the dough is perfectly set in the mold, then the artist fills the ash inside the mold. The dough takes the exact shape of the mold while doing this. The extra remaining dough in the mold is then cut using a sharp knife.
After all of this, the dough is removed from the mold and left to dry. After 1-2 days, when the dough has dried, the ash inside the dough is removed completely by using a small broom called “koochi”. The uneven and extra dough is then smoothened and scooped off by using an iron knife called “Patti”.
Smoothening Process
The process of creating blue pottery is very time-consuming and tough. It includes many stages, from making the dough for pottery to firing. It is a very long process.
Creating The Dough
Raw materials that are used to create the dough for Blue Pottery are quartz powder, Multani Mitti, shattered glass, Katria Gond, and Saaji. After choosing the raw material, Saaji, Katria Gond, leftover glass, and Multani Mitti must first be crushed and ground into a fine powder. These uncooked ingredients are then precisely weighed and mixed with water on a spotless surface. When well combined, a non-sticky dough is produced, and it is then allowed to rest for at least 7-8 hours before being utilized.
Constructing The Mold
Plaster of Paris is used to create molds. The desired forms and sizes are created as molds, which are subsequently dried. It is cast in molds to prevent cracking because using dough has its limitations. Particular goods, like vases, are made using one or two molds, and the castings are joined together with a little dough and water. If properly cared for, the molds can be utilized more often.
Making The Product
A small amount of the created pottery dough is taken and flattened like a round tortilla. Then the flattened dough is placed on the mold. The mold is then continuously wiggled by the artist to set the dough properly inside it.
When the dough is perfectly set in the mold, then the artist fills the ash inside the mold. The dough takes the exact shape of the mold while doing this. The extra remaining dough in the mold is then cut using a sharp knife.
After all of this, the dough is removed from the mold and left to dry. After 1-2 days, when the dough has dried, the ash inside the dough is removed completely by using a small broom called “koochi”. The uneven and extra dough is then smoothened and scooped off by using an iron knife called “Patti”.
Smoothening Process
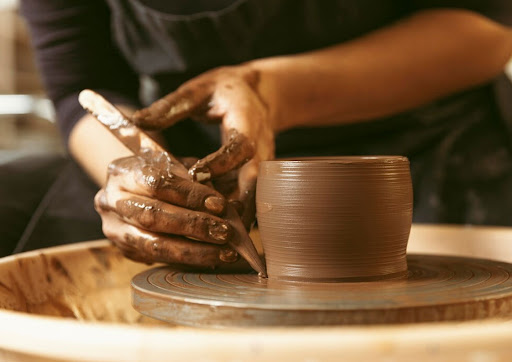
The rough edges of the dough are smoothened by using sandpaper or by rubbing the dough on a stone. The product is then coated by dipping it in the liquid dough and then again rubbed with the help of sandpaper. This process is repeated two times to create a seamless effect. Then the product is attached to the desired base. And then left to dry again.
Creating The Color
Oxides and Ferro metals are frequently used to create the colors in blue pottery. These oxides are offered in the market as little lumps. The oxide lumps are combined with chewable gum and ground into a powder. Edible gum is a binding agent.
Painting The Product
After the product attached to the base dries, the color is also ready then the product is ready to paint. Craftspeople adopt or occasionally create their own ideas to paint the dough. Every item is hand-painted. A fine brush or an artist’s brush developed especially for the job is used to first draw the outlines.
If the product is circular in shape, drawing an outline is simple; all that is needed is to lay the item on a potter’s wheel and lightly touch the brush tip to the object to create a clean line. After the outlines, colors are used to fill in the blanks and create the full design.
The Glazing Process
When the paint has dried and the product is ready, the glaze is applied. With certain proportions of numerous basic components, distinctive glazing is produced. It is made and heated to melt a mixture of boric acid, zinc oxide, potassium nitrate, powdered glass, and Borex.
The resulting lumps are again pounded into a fine powder once the mixture has cooled and formed lumps. Then, a slurry is made by mixing this powder with maida (flour) and water. After dipping the finished products in this solution, they are equally covered. The product is finally dried in the sun.
Firing The Final Product
Creating The Color
Oxides and Ferro metals are frequently used to create the colors in blue pottery. These oxides are offered in the market as little lumps. The oxide lumps are combined with chewable gum and ground into a powder. Edible gum is a binding agent.
Painting The Product
After the product attached to the base dries, the color is also ready then the product is ready to paint. Craftspeople adopt or occasionally create their own ideas to paint the dough. Every item is hand-painted. A fine brush or an artist’s brush developed especially for the job is used to first draw the outlines.
If the product is circular in shape, drawing an outline is simple; all that is needed is to lay the item on a potter’s wheel and lightly touch the brush tip to the object to create a clean line. After the outlines, colors are used to fill in the blanks and create the full design.
The Glazing Process
When the paint has dried and the product is ready, the glaze is applied. With certain proportions of numerous basic components, distinctive glazing is produced. It is made and heated to melt a mixture of boric acid, zinc oxide, potassium nitrate, powdered glass, and Borex.
The resulting lumps are again pounded into a fine powder once the mixture has cooled and formed lumps. Then, a slurry is made by mixing this powder with maida (flour) and water. After dipping the finished products in this solution, they are equally covered. The product is finally dried in the sun.
Firing The Final Product
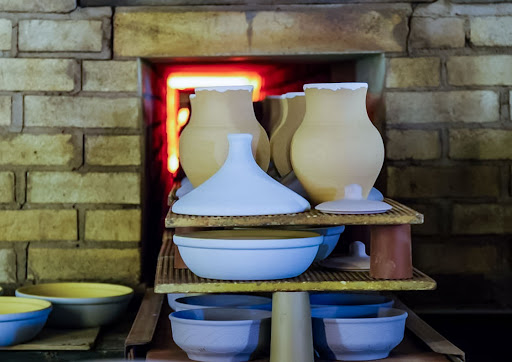
To dry them out, the items are kept in a furnace. The goods are carefully placed inside to prevent contact. To encourage even temperature dispersion inside the kiln, the center core of the structure is left exposed.
The kiln is sealed from the top and heated with charcoal and wood from the bottom. The firing must be controlled to be progressive and last for 4-5 hours because variations in temperature could lead to product cracks.
After the kiln has cooled for two to three days, the objects are removed. The finished Blue Pottery Vase – Lotus Bud is cleaned and packaged for the market after being isolated from the damaged ones.
The kiln is sealed from the top and heated with charcoal and wood from the bottom. The firing must be controlled to be progressive and last for 4-5 hours because variations in temperature could lead to product cracks.
After the kiln has cooled for two to three days, the objects are removed. The finished Blue Pottery Vase – Lotus Bud is cleaned and packaged for the market after being isolated from the damaged ones.