Madhuchishtavidhana or lost-wax method (cire perdue) described in the Shilpasastra in the treatise Manasara is a state-of-the-art technique used for creating Chola bronzes in South India. The figure is first fashioned in the hard wax and then covered with successive layers of clay till a thick solid coat is obtained. The clay-coated figure is then heated in an oven so the liquidated wax drains out.
The figure is first fashioned in the hard wax and then covered with successive layers of clay till a thick solid coat is obtained. The clay-coated figure is then heated in an oven so the liquidated wax drains out. Next, molten metal is poured into the hollow space thus created. It is allowed to cool sufficiently for it to solidify and then the outer shell is broken to reveal the metal image.
The metal image is then chiseled, filed and polished to achieve fine details and final look. While making large statues, a particular material is chosen, which would be lighter than metal but as durable. This serves as the central core of the wax model and remains within the final metal statue.
The figure is first fashioned in the hard wax and then covered with successive layers of clay till a thick solid coat is obtained. The clay-coated figure is then heated in an oven so the liquidated wax drains out. Next, molten metal is poured into the hollow space thus created. It is allowed to cool sufficiently for it to solidify and then the outer shell is broken to reveal the metal image.
The metal image is then chiseled, filed and polished to achieve fine details and final look. While making large statues, a particular material is chosen, which would be lighter than metal but as durable. This serves as the central core of the wax model and remains within the final metal statue.
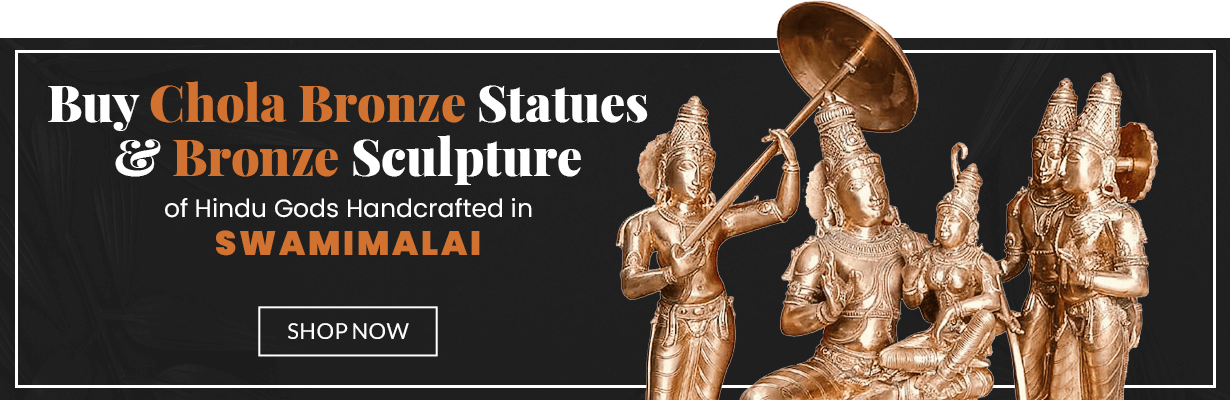
This technique helps in weight reduction of large statues. As evident from the above process, mass production of such images is not possible because each is created unique with loss of its original wax model.
The process starts with Sthapathy (sculptor) conceiving the form of the deity in his mind, which would be his subject. He meditates on this form through Dhyana Shlokas (invocation verses mentioned in scriptures) to establish a clear picture of the deity with all his/her physical attributes. As it may be obvious, sculpturing in Indian context is much more than just creating a statue. Every Sthapathy is required to have full grasp on Dhyana Shloka besides Neetisaaram, Amaram and Shilpasaaram. These represent the Moortis (Sanskrit term for sculpture) the Sthapathy aims to create. There are as many as 114 specifications given in Shilpashastra which are required to be adhered to while making an idol. It is also expected of a Sthapathy to be able to work out from general experience the proportions of various body parts with respect to overall height. The image so created is based on Sthapathy’s imagination but according to traditional standards followed by his forefathers passed on from generation to generation.
Bee wax is generally used for models if available. In case purified wax is used then it is hardened a bit by mixing it with resin and then melting it with groundnut oil.
Purified wax needs to be treated so being too flexible and semi-transparent. The molten mixture is then filtered and poured into cold water so it hardens to be used for preparing the wax model. The tools used for wax modeling are fashioned in sandal wood and are called Patula. They are broad in the middle with tapering ends and varying in sizes as per Sthapathy’s requirements.
The process starts with Sthapathy (sculptor) conceiving the form of the deity in his mind, which would be his subject. He meditates on this form through Dhyana Shlokas (invocation verses mentioned in scriptures) to establish a clear picture of the deity with all his/her physical attributes. As it may be obvious, sculpturing in Indian context is much more than just creating a statue. Every Sthapathy is required to have full grasp on Dhyana Shloka besides Neetisaaram, Amaram and Shilpasaaram. These represent the Moortis (Sanskrit term for sculpture) the Sthapathy aims to create. There are as many as 114 specifications given in Shilpashastra which are required to be adhered to while making an idol. It is also expected of a Sthapathy to be able to work out from general experience the proportions of various body parts with respect to overall height. The image so created is based on Sthapathy’s imagination but according to traditional standards followed by his forefathers passed on from generation to generation.
Bee wax is generally used for models if available. In case purified wax is used then it is hardened a bit by mixing it with resin and then melting it with groundnut oil.
Purified wax needs to be treated so being too flexible and semi-transparent. The molten mixture is then filtered and poured into cold water so it hardens to be used for preparing the wax model. The tools used for wax modeling are fashioned in sandal wood and are called Patula. They are broad in the middle with tapering ends and varying in sizes as per Sthapathy’s requirements.
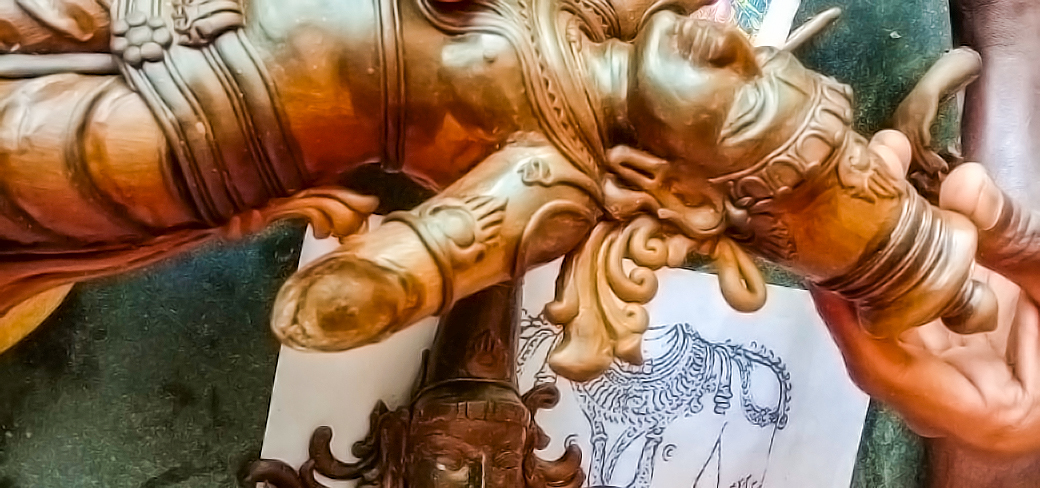
Sthapathy manually makes a rough outline of the parts of the body of the icon in wax. Details are worked on the rough outline with the help of Patulas. Throughout the process of model making, Sthapathy has to keep exposing the wax figure to a source of heat since the wax tends to get hardened. Wax modeling as a step is a crucial one because the final form of the statue will fully depend on the skill and visualization with which Sthapathy creates it. If this stage is executed with sufficient care and concentration then the final image emerges with great perfection saving Sthapathy all the time he may otherwise spend in remodeling the metal image with hammer and chisel.
After completing the wax model it is mounted on a wax base which is in turn attached to a wax rod in the shape of a funnel called the runner. This is to serve as an outlet for the molten wax when the clay mould is heated for casting. The Sthapathy also connects different sections of the image with wax rods to facilitate easy running of molten metal alloy into all parts simultaneously. Such rods also serve as additional support to the image when cast in metal while Sthapathy works on the cast model with hammer and chisel to impart finishing touches. The wax model is coated with finely ground clay in semi-solid paste and mixed with charred husk and cow-dung. The first coating is applied in a semi solution from and allowed to dry before second coat is applied. This process is repeated several times till a fine layer of loom is spread out over the entire wax model surface. It is important that no portion of the wax model escapes clay coating and its details are preserved exactly.
The clay should be of fine texture to preserve the intricate details of the model and strong enough to withstand the hot liquid metal pour. Clay from an anthill is preferred as an ideal choice for this purpose.
The model is then encased in several layers of coarser clay, each successive layer becoming coarser and bulkier. Finally a fine strip of steel or wire is tied around the entire clay mould, while taking care that the wax orifice that shall serve both as runner and vent while casting remains intact. When the clay mould is dry and strong enough to withstand subsequent operations, heating the mould over a drafted ground furnace clears the wax inside the mould. It melts and runs out which is then collected and weighed in order to ascertain the quantity of metal needed for casting.
The composition of the metal used for casting is Copper, Brass and Lead (the alloy is called Bronze). In olden days small quantities of Silver and Gold were added to make it Panchadhatu (five metals). Brass is added to reduce the melting temperature of the alloy and also to give a golden hue to the finished figure. Small quantity of lead is added just before casting to smoothen the pouring and make the alloy flexible and soft for easy application of chisel and hammer. Normally 20 parts by weight of copper is mixed with 5 parts of brass and 1 of lead. These metals are locally available in the form of scraps such as old unserviceable utensils, cuttings, wires, etc. Melting of the alloy is done in ceramic crucibles. The furnace generally used for melting is pit type, coke fueled, with lining of fire clay brick and can either be round or rectangular. A blower, manual or electric, is connected at one end to blow air. Before actual casting the mould should be heated sufficiently. A rough kiln is built around the mould and the fire is kept up by burning firewood and dung cakes till the mould turns red hot. This hardens the mould and expels traces of moisture.
After completing the wax model it is mounted on a wax base which is in turn attached to a wax rod in the shape of a funnel called the runner. This is to serve as an outlet for the molten wax when the clay mould is heated for casting. The Sthapathy also connects different sections of the image with wax rods to facilitate easy running of molten metal alloy into all parts simultaneously. Such rods also serve as additional support to the image when cast in metal while Sthapathy works on the cast model with hammer and chisel to impart finishing touches. The wax model is coated with finely ground clay in semi-solid paste and mixed with charred husk and cow-dung. The first coating is applied in a semi solution from and allowed to dry before second coat is applied. This process is repeated several times till a fine layer of loom is spread out over the entire wax model surface. It is important that no portion of the wax model escapes clay coating and its details are preserved exactly.
The clay should be of fine texture to preserve the intricate details of the model and strong enough to withstand the hot liquid metal pour. Clay from an anthill is preferred as an ideal choice for this purpose.
The model is then encased in several layers of coarser clay, each successive layer becoming coarser and bulkier. Finally a fine strip of steel or wire is tied around the entire clay mould, while taking care that the wax orifice that shall serve both as runner and vent while casting remains intact. When the clay mould is dry and strong enough to withstand subsequent operations, heating the mould over a drafted ground furnace clears the wax inside the mould. It melts and runs out which is then collected and weighed in order to ascertain the quantity of metal needed for casting.
The composition of the metal used for casting is Copper, Brass and Lead (the alloy is called Bronze). In olden days small quantities of Silver and Gold were added to make it Panchadhatu (five metals). Brass is added to reduce the melting temperature of the alloy and also to give a golden hue to the finished figure. Small quantity of lead is added just before casting to smoothen the pouring and make the alloy flexible and soft for easy application of chisel and hammer. Normally 20 parts by weight of copper is mixed with 5 parts of brass and 1 of lead. These metals are locally available in the form of scraps such as old unserviceable utensils, cuttings, wires, etc. Melting of the alloy is done in ceramic crucibles. The furnace generally used for melting is pit type, coke fueled, with lining of fire clay brick and can either be round or rectangular. A blower, manual or electric, is connected at one end to blow air. Before actual casting the mould should be heated sufficiently. A rough kiln is built around the mould and the fire is kept up by burning firewood and dung cakes till the mould turns red hot. This hardens the mould and expels traces of moisture.
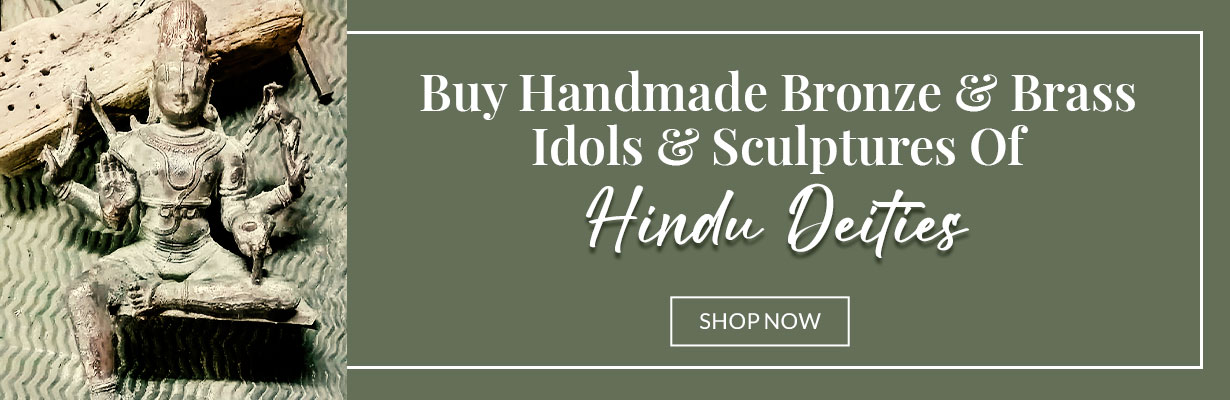
The mould is then buried in the earth up-to the mouth of the orifice to keep it firm and upright in position while pouring molten metal into it.
It also helps prevent premature and sudden cooling of the molten metal after filling the empty chamber caused by removal of wax from the clay mould.
For melting metal scraps are put into the crucible and melted to white heat in the coke furnace. The crucible with accurately weighed metal scraps is put in the furnace that is set alight. The air blower is turned on to help maintaining the heat and flames. Metal scrap is added to the molten alloy in the crucible periodically till the required quantity of metal is melted. When the metal has reached proper temperature and the clay mould also heated sufficiently, pouring (Casting) is done. Some protection in the form of rags etc. is spread around the orifice at the time of pouring to prevent metal spilling. Metal is generally poured in a thin stream. After the mould is completely filled with molten metal it is left to cool. Finally, the cast piece is then recovered by digging out the mould, cutting the binding strip or wire and breaking the clay layers. Sthapathy then proceeds on to the next step of chiseling and shaping. For finishing hammers, chisels, files and Seevuli are used extensively and for intricate work, finishing nails specially prepared by the Sthapathy himself are used. This is the stage at which the Sthapathy employs his skill in metal craft. He is the one who makes details in limbs, face, ornaments, dresses, etc. emerge on the rough metal cast. The process of polishing after finishing is quite laborious. It involves rubbing the surface with fine grade emery paper, which makes it very smooth.The image is cleaned in a solution of tamarind- water, polished and finally washed with soap-nut by brushing briskly with the help of wire-brush. This imparts a dazzling polish to the metal surface. The polished figure could then be oxidized black or brown as required.
It also helps prevent premature and sudden cooling of the molten metal after filling the empty chamber caused by removal of wax from the clay mould.
For melting metal scraps are put into the crucible and melted to white heat in the coke furnace. The crucible with accurately weighed metal scraps is put in the furnace that is set alight. The air blower is turned on to help maintaining the heat and flames. Metal scrap is added to the molten alloy in the crucible periodically till the required quantity of metal is melted. When the metal has reached proper temperature and the clay mould also heated sufficiently, pouring (Casting) is done. Some protection in the form of rags etc. is spread around the orifice at the time of pouring to prevent metal spilling. Metal is generally poured in a thin stream. After the mould is completely filled with molten metal it is left to cool. Finally, the cast piece is then recovered by digging out the mould, cutting the binding strip or wire and breaking the clay layers. Sthapathy then proceeds on to the next step of chiseling and shaping. For finishing hammers, chisels, files and Seevuli are used extensively and for intricate work, finishing nails specially prepared by the Sthapathy himself are used. This is the stage at which the Sthapathy employs his skill in metal craft. He is the one who makes details in limbs, face, ornaments, dresses, etc. emerge on the rough metal cast. The process of polishing after finishing is quite laborious. It involves rubbing the surface with fine grade emery paper, which makes it very smooth.The image is cleaned in a solution of tamarind- water, polished and finally washed with soap-nut by brushing briskly with the help of wire-brush. This imparts a dazzling polish to the metal surface. The polished figure could then be oxidized black or brown as required.
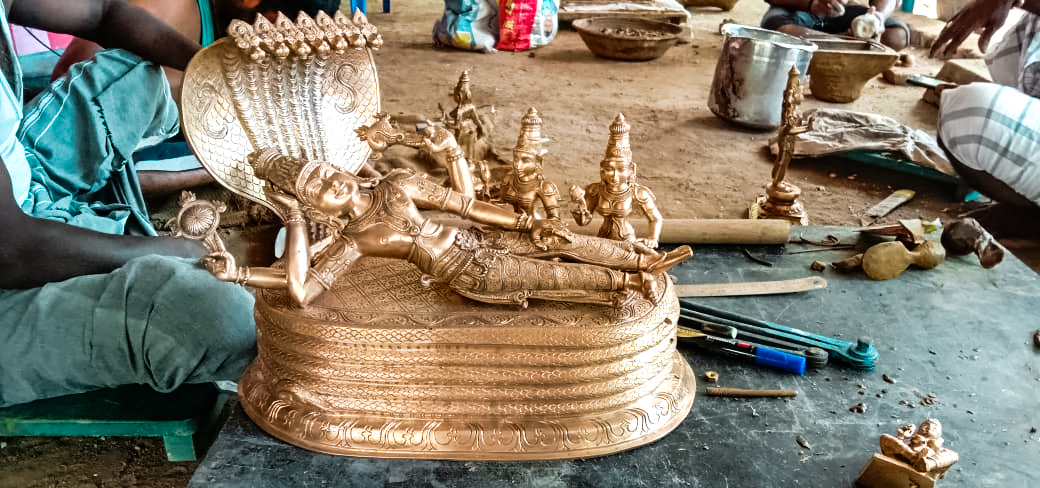